Towards a circular bioeconomy: lignin as a renewable alternative to chemical industry
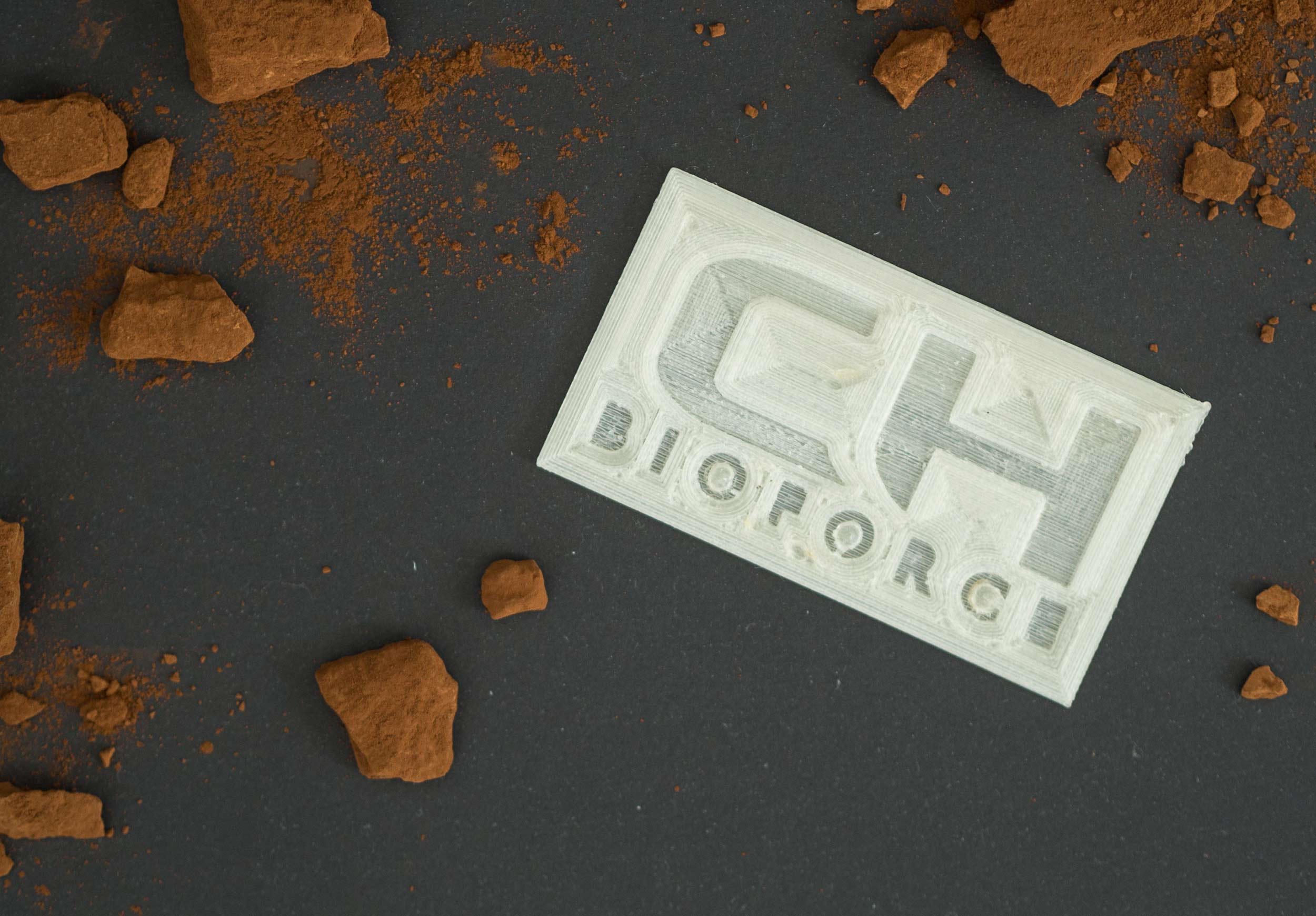
The chemical industry is almost entirely dependent on petroleum. Everyday products, from plastics, cosmetics and paints to adhesives and drugs are often made from oil. However, global challenges such as climate change and plastic pollution are now shifting the focus towards renewable and biodegradable raw materials.
Today a by-product, tomorrow a climate-neutral raw material
Along with cellulose and hemicellulose, lignin is one of the three main building blocks of biomass. Lignin is the only biomass constituent based on aromatic compounds, which makes it a potential feedstock for aromatic, supramolecular and other chemicals. It is therefore particularly promising as an alternative to oil-based raw materials used in the chemical industry. Compared to fossil petroleum, lignin derived from wood or even straw, for example, offers a more climate-friendly raw material.
Today, lignin is mostly produced as part of chemical pulping processes, namely Kraft and sulphite pulping. While cellulose/pulp is the main product, lignin is actually a by-product. 98 per cent of lignin is burnt for energy. Globally, this equates to approximately 50 million tons every year. The extraordinary material properties of lignin therefore mainly go unutilised.
On the other hand, technical lignin derived from commercial pulping processes is extensively altered in terms of its chemical makeup compared to native lignin. The most abundant aryl alkyl (β-O-4) ether linkages are readily fragmented and the structures further condensed due to the harsh pulping conditions. Lignin gained from kraft pulping, the pulping process most commonly used around the globe, also contains sulphur, which destroys the reactivity and material properties of commercially available lignins.
CH-Bioforce extracts all biomass components in the same process
CH-Bioforce has solved the problem in a fundamentally different way. We have developed a method which gently extracts all of the main components of biomass in one process. The resulting biomaterials – dissolving pulp, polymeric hemicellulose and sulphur-free lignin – are extremely pure and close to their natural form. Furthermore, our process can produce these high-quality biomaterials also from agricultural residue streams such as straw.
The structure and properties of the extracted lignin depend on the feedstock (softwood, hardwood, straw, etc.), type of fractionation process, and also the process parameters. Therefore, it is extremely important that lignins are properly characterised with an eye to specific process parameters in order to optimise their use in different applications.
Together with our academic and industry partners, we have conducted several studies to understand how the fractionation process and its parameters impact on the chemical structure of the resulting lignin and thus how they affect the material properties of the final product.
Findings from these studies were recently published here:
CH-Bioforce Oy
CH-Bioforce Oy is a Finnish start-up founded in 2016. The company’s innovative BIOFORSENSE® biomass fractionation technology dates back to 2011, when inventors Lari Vähäsalo, Nicholas Lax and Sebastian von Schoultz made their first findings. Today, the company forms part of the Chemec group, which operates in the chemical industry. CH-Bioforce currently employs ten members of staff. Our R&D and pilot plant is located in Raisio, Finland.
For more information, please contact:
Lari Vähäsalo, PhD
R&D Director, CH-Bioforce Oy